Het begon met Studebaker
Vandaag bouwt de fabriek de Audi Q8 e-tron en de Q8 Sportback e-tron. Maar sinds Pierre D’Ieteren in september 1948 de eerste steen legde, passeerden ruim acht miljoen auto’s van diverse merken en modellen de revue. In een bescheiden atelier begon Lucien D’Ieteren (de vader van Pierre) in de jaren dertig Amerikaanse Studebakers te assembleren. Hij had een eigen fabriek nodig en creëerde de ‘Anciens Etablissements D’Ieteren Frères’ op een terrein naast de spoorweg in Vorst. In april 1949 liep de eerste Studebaker (een Champion Sedan) van de band, al gebeurde er toen nog veel met de hand. Er kwamen maar vijftien auto’s per dag uit de fabriek.
In 1954 was de eerste Volkswagen Kever uit Vorst een feit. De fabriek breidde toen ook fors uit. Van 1954 tot 1962 werden 16.560 exemplaren van de legendarische Volkswagen Transporter T1 gebouwd. In 1960 stopte de productie van Studebakers en rolden er alleen nog Volkswagens en Porsches (de 356 Cabrio uit 1961) van de band. Meer dan een miljoen Passats, vier miljoen Golfs, meer dan een miljoen Kevers: de productieaantallen zijn indrukwekkend.
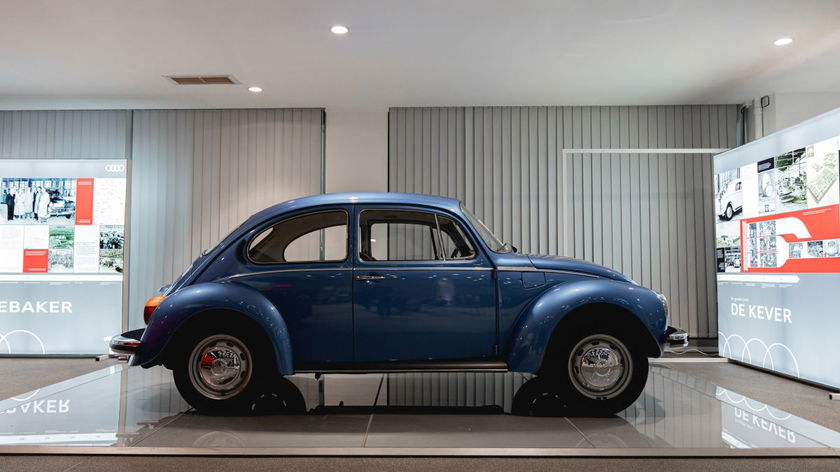
De Seat Toledo (1997) en Leon (1998), de Volkswagen Lupo (2001) en Polo (2006): allemaal werden ze op een bepaald moment in Vorst gebouwd. De eerste Audi uit Vorst was de A3 (2004). Pas in 2007 werd Volkswagen Vorst omgedoopt tot Audi Brussels. Drie jaar later werd het de exclusieve productiesite voor de Audi A1 (eerste generatie). En in 2018 werd Vorst de eerste Audi-fabriek met alleen nog 100 procent elektrische modellen.
Advertentie – lees hieronder verder
Kleinste Audi-fabriek
Binnen de multinational Audi is Audi Brussels de kleinste productievestiging, al moeten we dat nuanceren. De productiesite is immers veertig keer groter dan bij de start in 1949! De fabriek is zowat twee voetbalvelden breed en ligt in een lange strook tussen de Brits Tweedelegerlaan en de spoorlijn. De totale oppervlakte beslaat 563.321 m². Audi telt wereldwijd vijf eigen productiesites: Ingolstadt en Neckarsulm (Duitsland), Vorst (België), Györ (Hongarije) en San José Chiapa (Mexico). Lijkt jou dat weinig? Klopt, want als je er alle vestigingen van de Volkswagen-groep die ook Audi’s bouwen en de dochtermerken Bentley en Lamborghini bijtelt, dan kom je aan 21 productiesites in 12 landen. Audi Brussels bouwde in 2022 50.302 wagens, tegenover 192.991 wagens in Volvo Car Gent.
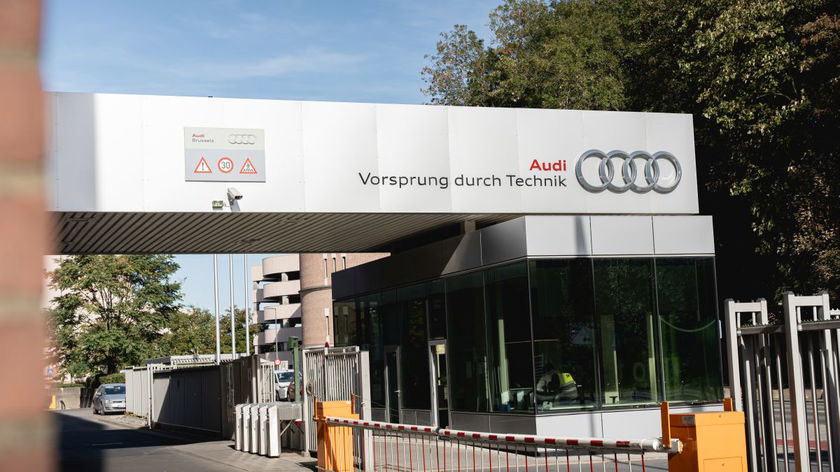
Gerecycleerde zitbank
De receptie van de fabriek bestaat uit een showroom met enkele modellen die ooit in Vorst gebouwd werden, zoals de Volkswagen Kever of de Volkswagen Passat GLS. Ook een opvallende zwarte … zitbank trekt hier de aandacht. Die is namelijk gemaakt van plastic uit het kanaal Brussel-Charleroi. In het schijnbaar zuivere water daar zit meer afval dan je zou denken. Een zogenaamde litter trap in de haven van Brussel verzamelt dit afval – tot 1,5 m³ per week – om het te recycleren. Zo werd uiteindelijk deze zwarte zitbank gemaakt met een 3D-printer.
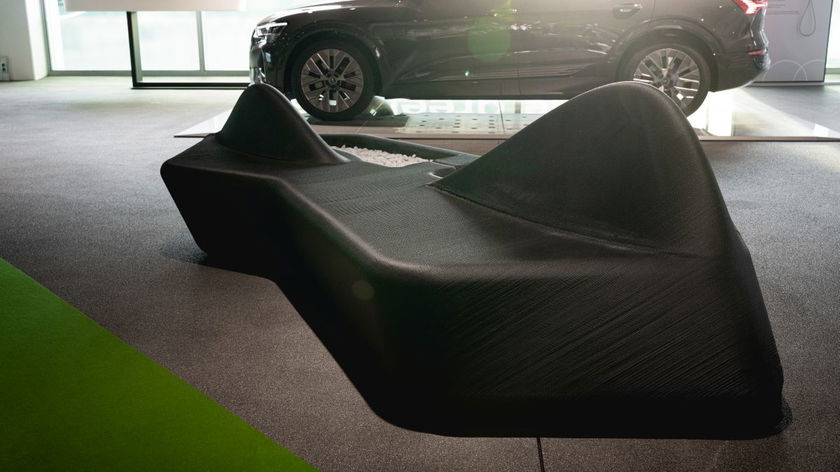
Eén kleur, verschillende locaties
Bij een luxewagen zoals de Audi Q8 e-tron hoort een perfecte koetswerklak. En dat is moeilijker dan je denkt. Verschillende onderdelen van het koetswerk worden namelijk op verschillende locaties gespoten maar moeten toch perfect matchen. De onderdelen komen van een handvol toeleveranciers. Zo wordt de bumpermodule in een bedrijf op enkele kilometers van de fabriek gemaakt en daar al meteen in de juiste kleur geverfd. Idem dito voor de handgrepen op de deuren bijvoorbeeld. Audi-medewerkers van de paintshop gaan naar de toeleverancier om de kleuren goed te keuren. De Q8 e-tron heeft trouwens losse delen uit aluminium (deuren, voorvleugels enzovoort) om het hoge gewicht van het batterijpakket (meer dan 700 kg) toch een beetje te compenseren.
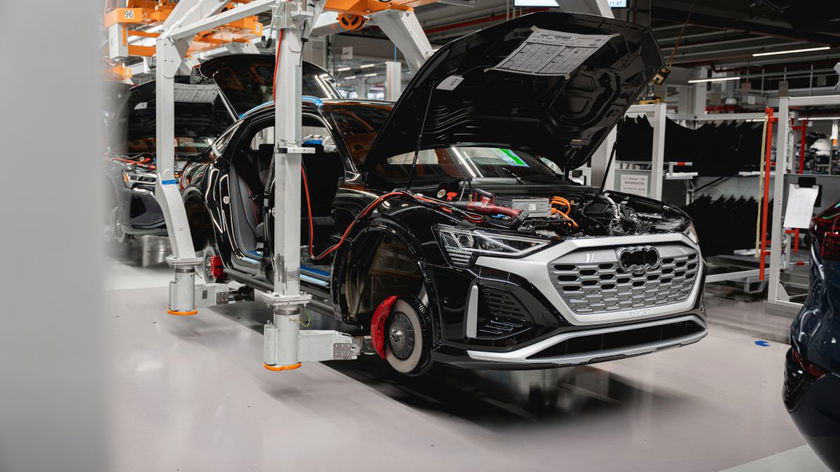
7 procent vrouwen
Bij Audi Brussels zijn 3.000 medewerkers aan de slag, van wie 7 procent een vrouw is. Werken in een autofabriek hoeft immers niet per se fysiek zwaar te zijn. In de fabriek rijden ook volledig geautomatiseerde transportrobots rond die de omgeving kennen en onderdelen naar de productielijn brengen. De onderdelen worden trouwens niet altijd per soort gegroepeerd, maar wel in de juiste sequentie volgens de volgorde van de auto’s die op de productieband passeren.
De medewerkers in de fabriek spreken drie talen. Naast Nederlands en Frans sluipt er ook weleens een Duits woord tussen, dat in onze eigen talen te verwarrend zou zijn. Denk maar aan Heckklappenverkleidung (de binnenbekleding van het kofferdeksel).
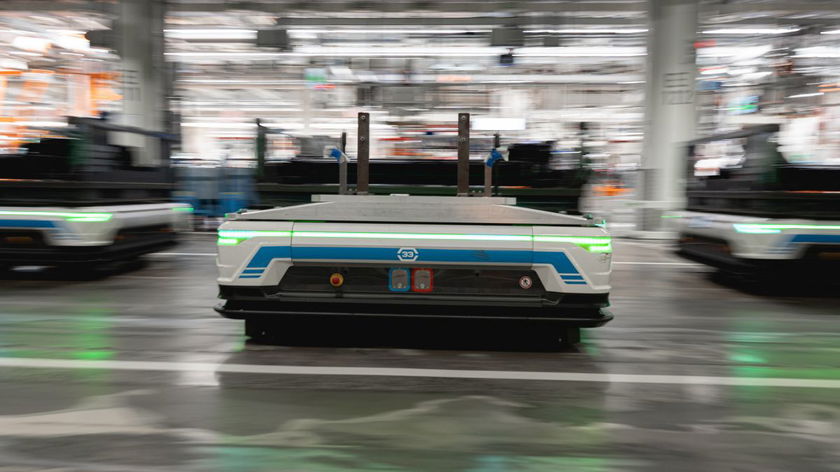
The Pink Panther
Ook The Pink Panther helpt mee tijdens het productieproces. Wanneer je door de fabriek wandelt, hoor je immers af en toe het deuntje van deze filmserie. Nee, dat betekent niet dat de medewerkers mogen pauzeren maar wel dat er zich ergens op de productielijn een probleem stelt. Als een medewerker een probleem opmerkt, kan hij of zij aan een koord trekken om hulp in te roepen. Het nummer van de betrokken werkpost kleurt dan geel of rood op de schermen langs de productielijn, zodat duidelijk wordt waar het probleem zich bevindt.
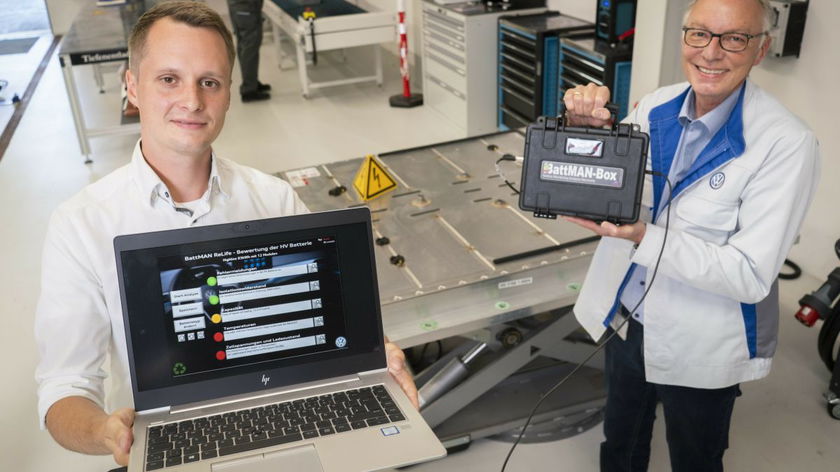
BattMAN
BattMAN helpt ook een handje. We hebben het dan niet over de actieheld, maar over software die ontwikkeld werd door de afdeling kwaliteitscontrole van Audi Brussels. De BattMAN-software (Battery Monitoring Analysis Necessity) zorgt voor een snelle en betrouwbare analyse van de hoogspanningsbatterij van de auto’s. Een computer met deze software controleert de state of health in enkele minuten tijd zonder de batterij te moeten openen. Zo wordt snel duidelijk welke modules of cellen bijvoorbeeld geschikt zijn voor recyclage. Intussen wordt het systeem door verschillende merken van de Volkswagen-groep gebruikt.

CO2-neutraal
De fabriek schenkt veel aandacht aan het milieu en is sinds 2018 CO2-neutraal. Dat betekent dat ze volledig op groene energie draait. Op het dak ligt 107.000 m² aan zonnepanelen en daar komt dit jaar nog 18.000 m² bij. Zowat een vierde van de oppervlakte van de fabriek wordt dus bedekt met zonnepanelen. Er komt binnenkort ook een windturbine op de site en biogas zorgt voor de verwarming.
Over CO2 gesproken: de batterijcellen van de Q8 e-tron worden in Györ (Hongarije) gemaakt en komen nu via de trein naar Vorst. Dat bespaart 2,6 ton CO2 per jaar, het equivalent van vijftien vrachtwagens die elke dag 1.300 km moesten rijden. Daarnaast wordt gebruikt water behandeld zodat het hergebruikt kan worden, goed voor een waterbesparing van drie olympische zwembaden per week. En 57 procent van het afval dat de fabriek produceert, wordt gerecycleerd, bijvoorbeeld tot pellets die de staalindustrie in ovens kan gebruiken.
Op zoek naar een auto? Zoek, vind en koop het beste model op Gocar.be